Lubricators apply a controlled amount of lubricant to areas of friction on rotating or moving mechanical parts. Since bearings, dies, chains, cables, spindles, pumps, railways, and gears need to be lubricated for equipment to function smoothly and dependably, lubricating systems are essential to manufacturing and industrial businesses. Read More…
OPCO Lubrication Systems, Inc. has been a leading manufacturer of lubrication products and systems for almost fifty years. Our products include lubrication pumps, air operated oilers, electric oilers, conveyor greasers, lubricants & greases, conveyor cleaners, and more. With our world class customer service and worldwide network of suppliers, OPCO is there around the clock to help. Visit our...
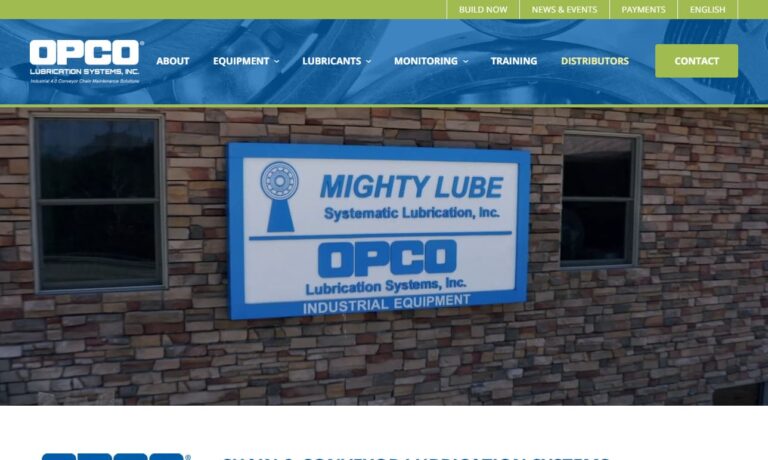
When it comes to grease dispensers we are the experts! It is our goal that we provide the highest quality custom products in the industry to ensure that we achieve full customer satisfaction every time. We are committed to providing quick turnaround times in order to get your products back to you so we may assist you in keeping your business moving along! Fill out the easy contact form on our...
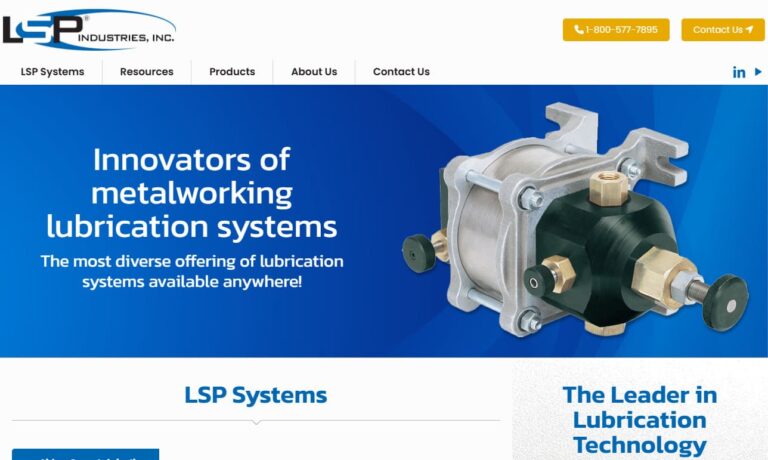
Pulsarlube U.S.A. produces manual, semiautomatic and fully automatic lubricating systems as well as centralized lubrication systems. We provide top-quality lubrication systems throughout the U.S., and we lead the global industry in the manufacture of automatic single-point lubricators.
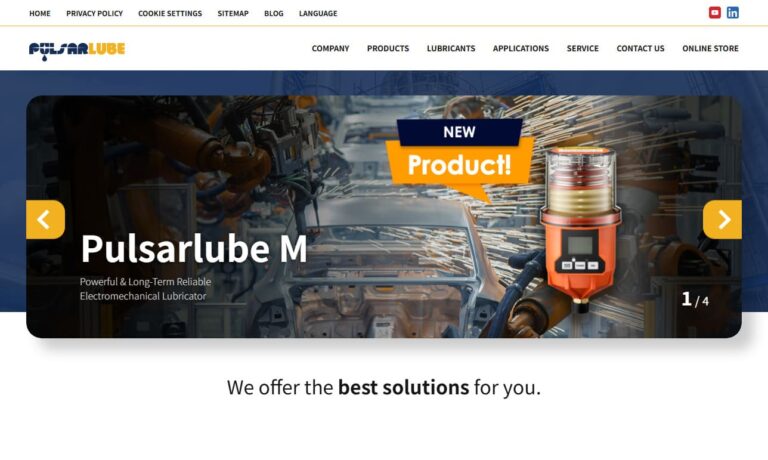
At Trico Corporation, we specialize in providing innovative lubrication systems designed to optimize equipment performance and extend operational lifespan. Our commitment to excellence drives us to engineer and deliver solutions that address the diverse needs of industries worldwide. We focus on precision, ensuring that our systems enhance efficiency, reduce downtime, and minimize wear on...

At American Lubrication Equipment Corporation, we specialize in providing advanced lubrication systems designed to optimize equipment performance and ensure operational efficiency. Our expertise extends to delivering high-quality products that address the diverse needs of industries relying on precise and reliable lubrication.
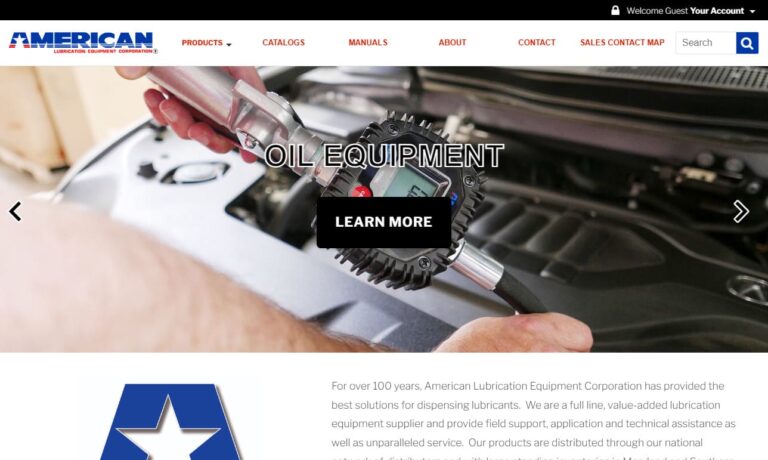
More Lubricator Manufacturers

Lubricator Design
The reservoir, pump, and filter are the three major components of lubricating systems. The old lubricant is stored in the reservoir after being consumed and then transferred by the pump to the system's necessary locations for lubrication. The filter keeps the system running smoothly by removing impurities from the lubricant.

Types of Lubrication Systems
Single-line Resistance
A central pump disperses the lubricant to one or more supply lines that are parallel to one another in single-line resistance (SLR) lubrication systems. These oil lubrication systems, which are low-pressure systems, are used for light and medium machines. The range of the oil pressure is 100 to 250 psi. These lubrication systems have a 100-point lubrication capacity. While the machine is in use, the oil flow is carefully controlled and distributed to the necessary machine parts.
Dual-line Lubrication
Dual-line lubrication systems use the two-phase alternating cycle, sometimes called deadline or double-line lubrication systems. The lubricant is injected from the reservoir to the first supply line during the first cycle, which causes all of the injectors' intake and discharge pistons to move in the same direction. Additionally, the lubricant is discharged in one direction. The two supply lines share the injectors, which are set up in a modular fashion.
Positive Displacement Injector Lubrication Systems
A central pump drives positive displacement injector (PDI) lubrication systems, which create pressure (more than 55 bars) to spread the oil throughout several supply lines. After that, the lubricant is applied to the feed lines, where PDIs are mounted. The fixed displacement piston inside the PDIs is moved hydraulically against spring pressure once the operative pressure is attained to discharge a fixed amount of lubricant into the lubrication point. Small- to medium-sized machinery with PDI lubrication systems are used when several lubrication sites must be precisely and accurately dispensed with lubricant. Systems for PDI lubrication can be programmed to release lubricants at predetermined intervals.
Series Progressive Lubrication Systems
The master divider block, which distributes the lubricant to secondary divider blocks, is connected to the pump in a series of progressive lubrication systems. In divider blocks, the necessary lubrication is delivered by several hydraulically operated spool valves organized in a modular fashion. Since the lubricant is dispensed from each valve in series, the lubricant on one valve will release after the discharge of lubricant from the valve before it. As a result, the divider block operates flawlessly if the final valve releases the right amount of oil. But if one valve is broken, the divider block won't disburse the lubricant properly, leading to pressure buildup.
Types of Lubricants
Grease and oil are the typical lubricants released by lubricators, while other lubricants are also available. The semisolid, soap-and-oil-based grease is frequently used in difficult-to-reach spots because it lasts for a long time and only occasionally needs replenishing. Liquid lubricants that are simple to apply but provide essential protection against wear and corrosion for a machine in constant motion are known as oil lubricants. They are frequently mineral-based compounds like petroleum. When lubricants are discarded improperly, they may not all be environmentally sound.
Lubricant Components
Grease Lubricants
Oil, a thickening agent, and additives with self-lubricating qualities, like PTFE, graphite, and molybdenum disulfide particles, all combine to form grease. Due to their increased stickiness, grease lubricants adhere to surfaces more effectively. They shield the lubricated machine components' surfaces from deterioration and damage.
Dry Lubricants
Small, self-lubricating particles like PTFE, graphite, and molybdenum disulfide make up dry lubricants. When sprayed over the machine part's surface, these particles produce a tiny, slick layer. Dry lubricants can be combined with water, alcohol, or solvent and sprayed together; eventually, the mixture will evaporate, leaving the thin lubricating film on the surface. Dry lubricants do not draw dust or grime, unlike oil and grease.
Dry lubricants are employed for machine parts needing high accuracy, like actuating ball screws, lead screws, and gears. They can be found in hinges, locks, bearings, and threaded rods. Since oils oxidize at high temperatures, they are the greatest choice for high-temperature applications. However, because these lubricants can be wiped away, they are not the best when the lubrication point is exposed to liquids and solvents.
Gear Lubricants
Gear lubricants are made specifically to prevent abrasion on the gears and their gear teeth. These lubricants must be thermally stable to stop sludge buildup on the gears. Gear lubricants can be used with special additives to guard against localized corrosion and pitting on the gear teeth. To protect the surfaces from high pressure during shock loading, certain gear lubricant formulations use extreme pressure (EP) additives; EP additives are necessary for lubricants for gears inside strongly loaded gearboxes.
What to Consider When Buying Lubricators
Factors including capacity, pressure, flow rate, and maximum operating temperature should be considered when choosing a lubricating system. There are manual and automatic lubricators. Central lubrication systems (which are connected to the enormous machinery they maintain automatically by preprogramming) are particularly common in large industrial settings. Even though they can be connected to automatic systems like air lubricators, grease pumps are an example of manual lubricators. There is a lubricator to do the job, whether designed for spot lubricating machinery or for keeping a particular item, like a chain, consistently oiled or greased.

Choosing the Correct Lubricators Supplier
To make sure you have the most positive outcome when purchasing Lubricators from a Lubricators Supplier, it is important to compare at least 4 or 5 Suppliers using our list of Lubricators manufacturers. Each Lubricators Supplier has a business profile page that highlights their areas of experience and capabilities and a contact form to directly communicate with the manufacturer for more information or request a quote. Review each Lubricators business website using our proprietary website previewer to get an idea of what each company specializes in, and then use our simple RFQ form to contact multiple Lubricators businesses with the same message.